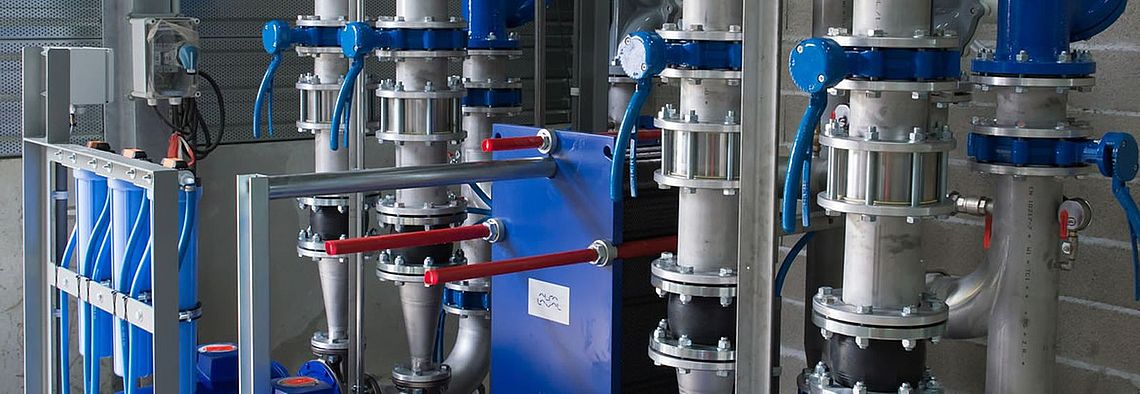
Your contact for Ring-Joints
Demands on form accuracy and surface quality are high
Ring-Joints RTJ
Ring-Joint (RTJ) gaskets are made from metallic materials. The requirements in terms of dimensional accuracy and surface quality are therefore high. This relates to both the gasket and the sealing section of the flange. The necessary surface quality depends substantially on the Brinell hardness of the gasket material The relationship RZ [µm] < 300/HB provides a useful indication. A distinction is made between two kinds of ring joint gaskets and two different calculation methods are therefore used:
1. RTJ gaskets with osculating radius
a) The convex octagonal RTJ gaskets, Profile AR 13, in which the convex cone case surfaces of the gasket are pressed against the even cone case surfaces of the groove when tensioned.
b) The oval ring-joint gasket, Profile A11, in which the circular surface is pressed against the cone case surfaces of the groove.
The sealing surface pressure increases or decreases to a lesser extent in response to any change in the bolt load.
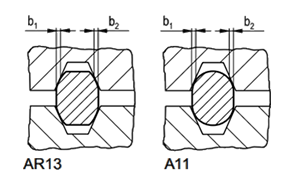
2. RTJ gaskets with flat sealing surfaces
The octagonal RTJ gasket, Profiles A13 and A14, are flat gaskets in which the sealing surfaces are two cone case surfaces. The projection in the direction of the bolting force bG = b1 + b2 should be set as the sealing surface width.
The sealing surface pressure increases or decreases proportionally in response to any change in the bolt load.
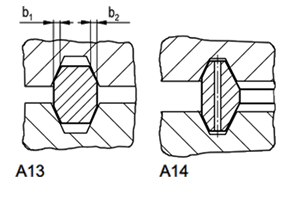
The application thresholds values of oval octagonal RTJ gaskets can be more accurately calculated in relation to material, diameter, pressure, temperature and the surface pressure limits. Here the fictitions sealing characteristic values in accordance with AD are replaced with the values of σv and σ .ϑ Ring joint gaskets in accordance with API and ASME standards are mainly used in the petrochemical industry and in refineries as a reliable gasket for production pipelines. We are permitted to give our products the API Monogram. This guarantees that our products meet the latest API standards. It should be noted that in Profile A12 the flanges have metalto-metal contact. Profile AR13 with convex sealing surfaces. Ring joint gaskets can be produced as blind gaskets in Profile A11S, A13S etc. or as blind spectacle gaskets in Profile A11BS, A13BS (see Blind Gaskets).
Code designation | Material no. | Hardness (HB) | US-Type AISI | Code |
---|---|---|---|---|
Pure iron, e.g. Armco | 1.1003 | 90-100 | Soft-Iron | D |
Stw24mod | – | 90-100 | Soft-Iron | D |
Low-carbonsteel | – | 120 | Low-Carbon-Steel | S |
13 CrMo 4 4 | 1.7335 | Ca. 160 | – | 7335 |
12 CrMo19 5 mod | 1.7362 mod | Ca. 130 | 501 | F5 |
X6 Cr 13 | 1.4000 | Ca. 160 | 410 | S410 |
X5 CrNi 18 10 | 1.4301 | Ca. 160 | 304 | S304 |
X5 CrNiMo 17 12 2 | 1.4401 | Ca. 160 | 316 | S316 |
X6 CrNiTi 18 10 | 1.4541 | Ca. 160 | 321 | S321 |
X6 CrNiNb 18 10 | 1.4550 | Ca. 160 | 347 | S347 |
X6 CrNiMoTi 17 12 2 | 1.4571 | Ca. 160 | 316 Ti | 316 Ti |
Gasket cross-section
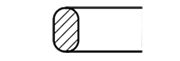
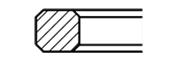
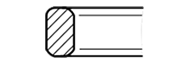
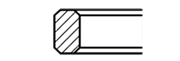
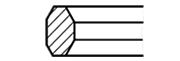
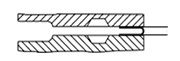
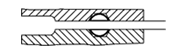
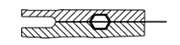
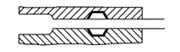
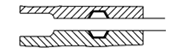
With the addition of a protective ring made from sheet metal to Profile F22, disruptive turbulence and accretions are avoided. At small edge widths the protective gaskets are symmetrical, at larger edge widths they are centred on one side. We can supply soft-iron compensating caps for damaged grooves, such as Profile AK11, AK12, AK13, AK14.
For a complete estimate on sealing flange connections, our efficient sealing estimate service is available.
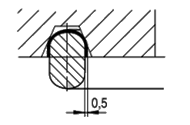

Profile
A11, A11S, A11BS, A12, A13, A13S, A13BS, AR13, AR13S, AR13BS, A14
Materials | Iron 1.1003 Stw24mod | Heat-resistant mild steel 1.5415 | Heat-resistant mild steel 1.7362 | Stainless Steel 1.4541 | Stainless Steel 1.4828 | Carbon steel copper-plated | Stainless steel 1.4541silver-plated | Copper2.0090 | Monel 2.4360 | ||
---|---|---|---|---|---|---|---|---|---|---|---|
Recommended max. roughness of the flange surfaces | µm | von bis | 3,2 6,3 | 3,2 6,3 | 3,2 6,3 | 1,6 3,2 | 1,6 3,2 | 3,2 6,3 | 6,3 12,5 | 3,2 6,3 | 3,2 6,3 |
Surface pressure limits for 20 °C | N/mm2 | σv σϑ | 235 525 | 300 675 | 400 900 | 335 750 | 400 900 | 135 600 | 100 750 | 135 300 | 260 660 |
E modulus at 20 °C | kN/mm2 | 210 | 210 | 210 | 200 | 200 | 210 | 200 | 128 | 178 | |
Surface pressure limits for 300 °C | N/mm | σv σϑ | 235 315 | 300 585 | 400 730 | 400 750 | 400 750 | 135 390 | 100 630 | 135 150 | 260 650 |
E modulus at 300 °C | kN/mm2 | 185 | 185 | 190 | 186 | 186 | 185 | 186 | 114 | 175 |